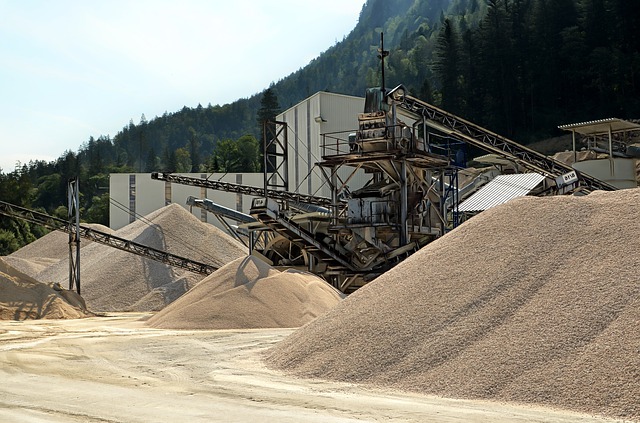
Impianti di frantumazione e alta tecnologia
In edilizia, un importante passaggio della lavorazione è costituito dalla preparazione delle malte (impasti composti dai cosiddetti leganti e acqua, oppure con l’aggiunta di materiali inerti e di sabbia). In questa fase, sono fondamentali gli inerti, elementi di origine rocciosa che possiedono una particolare caratteristica: non partecipano alle reazioni grazie alle quali il legante favorisce l’indurimento della miscela. Il procedimento di preparazione delle malte è il seguente: gli inerti vengono sciolti nella malta con l’acqua; in questo modo si innesca una reazione legante che porta alla formazione di un conglomerato solido che, andando avanti nel tempo, diventa sempre più resistente agli sforzi.
Gli inerti, quindi, non hanno una funzione legante ma, durante la fase di indurimento della malta svolgono un altro importante compito: riducono le fessure all’interno del composto e, così facendo, diminuiscono la quantità di legante necessaria al processo. Dato l’elevato costo del legante, questa sua diminuzione (dovuta, lo ricordiamo, alla presenza del materiale inerte) garantisce anche una significativa riduzione di spesa. Ma torniamo all’antefatto di questo processo; alla “creazione”, cioè, degli inerti.
Per ottenere grandi quantità di questi elementi, occorre rompere blocchi di pietra, di calcestruzzo o di altri materiali utilizzati nella costruzione, in modo da ottenere pezzi di materiale pietroso sempre più piccoli (fino alla definizione di granelli dalla granulometria prescelta in base alle diverse esigenze). Questo processo si attua all’interno dei cosiddetti impianti di frantumazione. I macchinari utilizzati per svolgere il lavoro di frantumazione sono detti frantumatori (o mulini); essi procedono alla distruzione dei grossi blocchi di pietra utilizzando l’energia meccanica. Anche l’industria mineraria li utilizza, ma lo fa con un obiettivo un po’ diverso: frantuma grossi blocchi di roccia per renderli più piccoli ed estrarre più facilmente il minerale in essi contenuto. I frantumatori attuali sono macchinari costruiti sulla base di tecnologie altamente innovative che riescono ad ottenere risultati impensabili fino a qualche tempo fa sia in termini di tempo di esecuzione, che per quanto riguarda il materiale ottenuto alla fine dell’intero procedimento di frantumazione (molto meglio definito, rispetto al passato).
Le fasi della frantumazione
La produzione di materiali inerti attraverso la frantumazione delle rocce prevede una serie di fasi lavorative che si susseguono fino all’ottenimento del risultato finale. Questi passaggi, detti fasi della frantumazione, sono quattro e si svolgono in quest’ordine:
- abbattimento del fronte di cava;
- frantumazione;
- vagliatura;
- lavaggio (eventuale).
In questa sede ci occuperemo solo del secondo passaggio; quello relativo alla vera e propria frantumazione del materiale roccioso.
Vari tipi di frantumazione
La frantumazione delle rocce, ossia l’azione meccanica disgregatrice, può essere ottenuta tramite procedimenti diversi.
- schiacciamento del pietrame: i pezzi di roccia vengono inseriti tra due robuste ganasce che, chiudendosi, li rompono, dividendoli in pezzi più piccoli;
- urto violento dell’elemento da frantumare: i massi ancora interi vengono scagliati con forza contro una parete molto dura e resistente;
- triturazione dell’inerte: in questo caso la frantumazione è il risultato del movimento di elementi resistenti (palle pesanti, barre) insieme allo stesso materiale inerte.
Chiaramente, ciascuna di queste modalità di frantumazione è ottenuta tramite macchine frantumatrici (frantoi) di tipo diverso. Quando una roccia subisce il passaggio all’interno di un frantoio, comincia ad essere disgregata in elementi dal diametro sempre più ridotto. Per arrivare alla dimensione più piccola, passando dalle pezzature più grandi (pietrisco), alle più piccole (sabbia), occorrono diversi stadi, successivi l’uno all’altro. In pratica, il materiale che viene fuori dal primo frantoio, alimenta una seconda macchina frantumatrice; e così via, secondo il seguente schema:
- frantumazione primaria: il pietrame proveniente dalla cava viene introdotto nel frantoio e ne esce con dimensioni massime superiori ai 70 mm (pezzature ancora troppo grandi per poter essere utilizzate);
- frantumazione secondaria: riduce ulteriormente il materiale proveniente dalla frantumazione primaria, ottenendo piccoli pezzi di dimensione compresa, all’incirca, tra 6 e 70 mm (il cosiddetto pietrischetto e la graniglia);
- frantumazione terziaria e macinazione: il materiale proveniente dalla frantumazione secondaria, subisce un ulteriore riduzione di diametro arrivando alla dimensione massima pari a circa 2 millimetri (sabbia e filler).
Tipologie di impianto di frantumazione
Esistono tre diversi tipi di impianto di frantumazione:
- impianti di frantumazione fissi: come intuibile, si tratta di impianti che, una volta installati in un posto, non vengono più spostati. Sono molto grandi e capienti e sono in grado di effettuare cicli produttivi completi;
- impianti di frantumazione semi-mobili: sono impianti a metà tra i frantoi fissi e quelli mobili. Possono essere trasportati solo nel momento in cui vengono smontati e sono in grado di rispondere alle esigenze di aziende di media grandezza;
- impianti di frantumazione mobili: sono quelli che si utilizzano più spesso perché sono più versatili e adattabili (come configurazione ed equipaggiamento) alle esigenze di produzione. La loro peculiarità principale è che sono dotati di cingoli (o di gomme) che consentono spostamenti rapidi e di semplice esecuzione.